Technical Innovations
THE CSM DIFFERENCE
Decades of experience in industrial construction taught us: Never assume that the job conditions will be in our favor. Limited access? Crowded job site? High Elevation? We bring our engineering skills to solve the problem unique to your project. The results: improved schedule, higher safely and a more efficient use of your budget.
Here are just 4 examples:
SWING STAGE SUSPENDED SCAFFOLDING
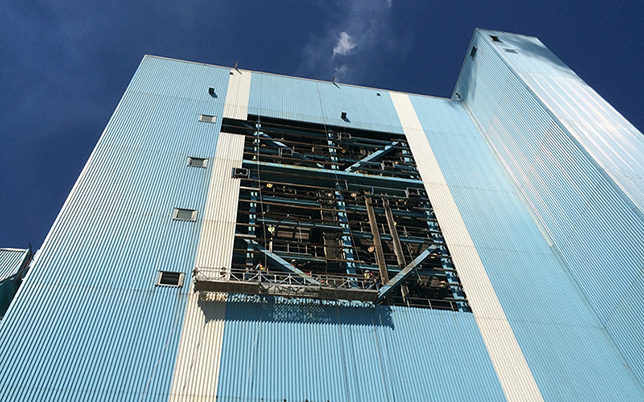
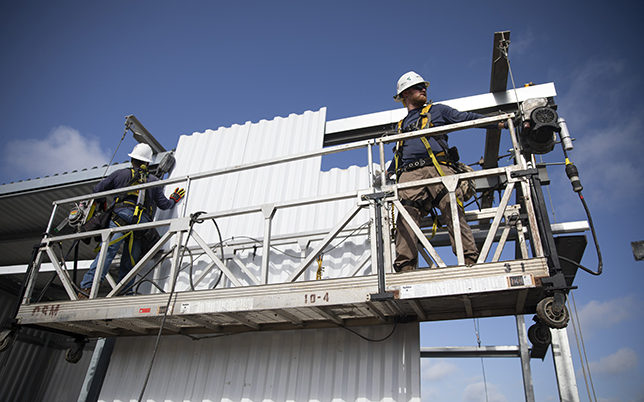
The Challenge
Many industrial structures are surrounded by obstructions. Often, walls are inaccessible due to other structures or civil work. Most siding contractors request modular scaffolding to be built when they cannot access the wall by manlift, which adds time and cost to the project.
The Innovation
CSM has invested in swing stage scaffolding equipment and training. Our foremen and leads are certified by the manufacturer to set up and operate swing stage scaffolding. When you contract CSM, we bring our equipment and trained team, allowing faster turnaround and lower scaffolding cost.
ENGINEERED TROLLEY
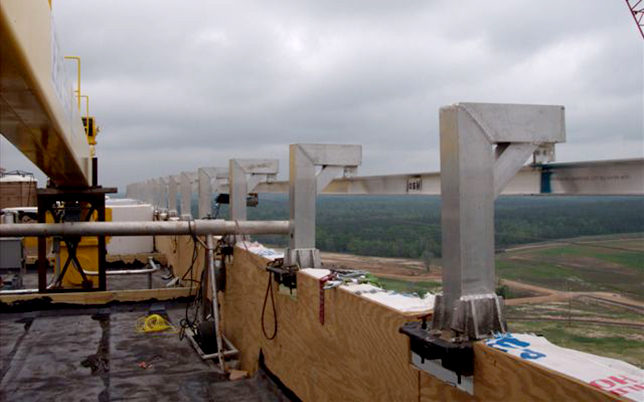
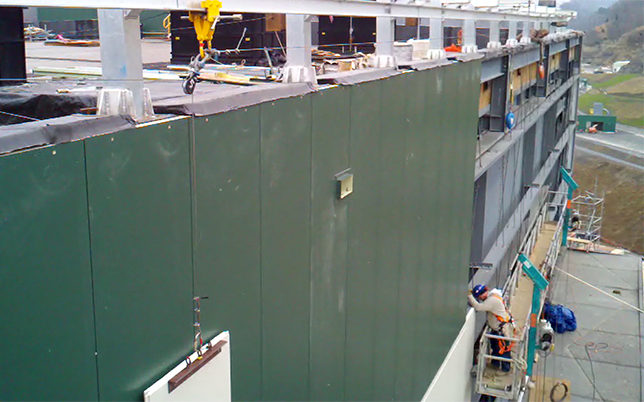
The Challenge
A power plant in Virginia needed insulated metal siding. Upon the initial site visit, we identified one wall that required a massive crane to lift the siding in place. Big cranes add significant time and cost to a project.
The Innovation
CSM designed and engineered a trolley system that allowed our panels to be lifted vertically and then transported horizontally over to our work area. This saved our client significant crane time and costs.
On-site roll forming capabilities
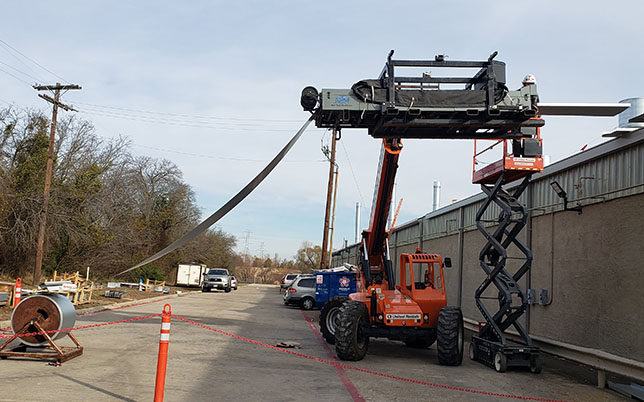
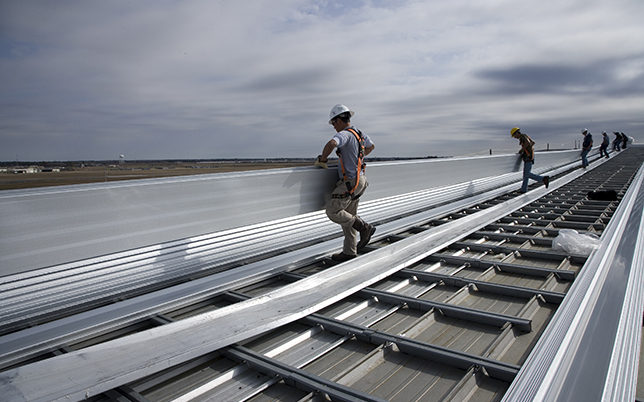
The Challenge
Metal roof manufacturers are limited to transporting panels up to 50’ long. Any metal roof over 50’ requires panels to be lapped and sealant is used to prevent water leakage. But, over time, the lap locations invite leaks.
The Innovation
CSM has the capabilities to roll form standing seam panels directly at your job site. We have installed continuous standing seam panels up to 175’ in length with no lap. No lap = no leak!
ENGINEERED WORK PLATFORM
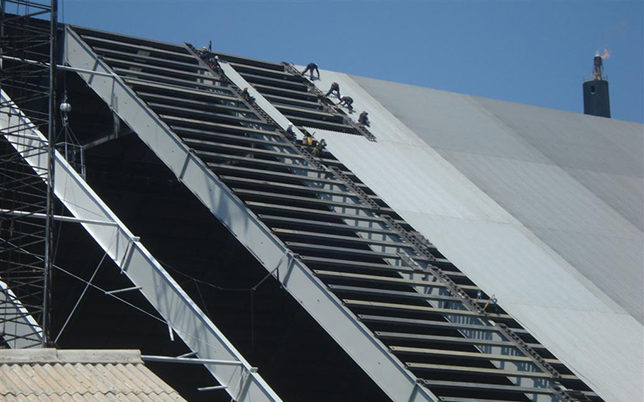
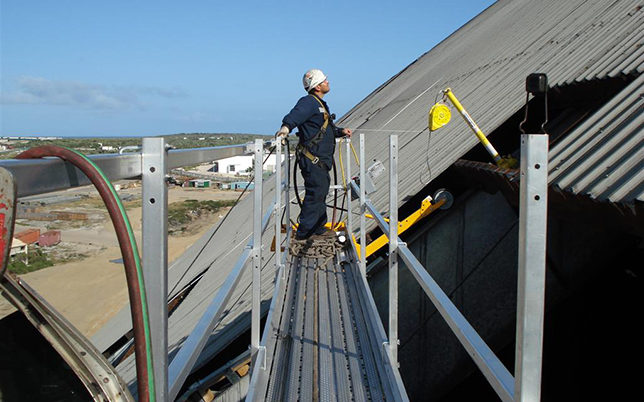
The Challenge
Valero needed a new roof in their Aruba facility. Their existing 45-degree roof was steep and severely corroded, creating an unsafe work environment and making it difficult to stage and secure panels during work.
The Innovation
CSM designed and engineered an access platform that gave our workers a level working area. Additionally, we engineered equipment that allowed panels to be lifted and safely secured during work.